Unlocking the European Market: The CE Risk Assessment
- David Connor
- Jul 22, 2024
- 8 min read
Updated: Jul 31, 2024
The third article in a six part series on CE marking

Product Development for the European Market
Developing products for the European market requires a proactive approach to safety and reliability. In line with the quality management principles of ISO 9001:2015, anticipating and mitigating product risk is paramount. By systematically identifying potential hazards and implementing safeguards, manufacturers can create products that meet stringent safety standards. Central to this process is risk assessment, a fundamental component of CE marking that ensures products are safe for their intended use and comply with European regulations.
What is Risk?
In terms of product CE marking, it is important to understand what is meant by the term risk:

Risk is any potential hazard to people, property, or domestic animals caused by your product, its use, misuse, or disposal.
Risk identification involves specifying the factors that could directly cause or lead to a potential hazard. For examples of common hazards encountered with commercial and industrial products, see the Hazard Examples section of this document.
What is a Product Risk Assessment?

A CE risk assessment is a systematic process of identifying potential hazards, analyzing the foreseeable risk associated with those hazards, then reducing the risk to an acceptable level.
The risk assessment includes identifying foreseeable risk throughout the product's lifecycle, from manufacturing to use, maintenance, service, and disposal.
Most European directives include some requirement that the manufacturer (or authorized representative) review and document an assessment of the product risk(s). Some directives, such as the Machinery Directive are very specific about a more formal and systematic approach to risk reduction (see Annex I).
For more information on EU directives, see Unlocking the European Market: Navigating Directives and Standards for Your Product.
The Risk Assessment Process
If you Google 'risk assessment template', you will quickly find out that there is no 'one size fits all' strategy for performing a product risk assessment. The process will often be tailored to a product type and the amount of risk inherent in that product.
There are several common concepts when developing a structured approach to identifying, evaluating, and mitigating potential hazards associated with a product that should be included in any risk assessment.
Hazard Identification:
The Hazard Examples section of this document gives some examples of common hazards associated with commercial and industrial products.
Identify potential hazards related to the product, including electrical, mechanical, chemical, and ergonomic risks.
Consider the product's intended use, foreseeable misuse, and the environment in which it will be used.
Risk Evaluation:
Determine if the identified risks are acceptable or if further action is required. A Failure Mode and Effects Analysis is often helpful in this evaluation process.
Compare the identified risks to safety standards and legal requirements.
Risk Reduction:
Implement measures to eliminate or reduce identified risks.
Prioritize risk mitigation efforts based on the risk level.
Consider design modifications, protective measures, warnings, or user instructions.
Risk Communication:
Clearly communicate identified risks and mitigation measures to relevant stakeholders, including users, operators, and maintenance personnel.
Provide appropriate safety instructions and warnings.
Documentation:
Maintain comprehensive documentation of the risk assessment process, including hazard identification, risk analysis, evaluation, mitigation measures, and decision-making.
Failure Mode and Effects Analysis
The Failure Mode and Effects Analysis (FMEA) is a systematic approach to identifying potential failures in a system, process, or product and analyzing the potential effects of those failures. The FMEA is often used in product risk assessment, since it is a critical tool for assessing risk and identifying potential problems before they occur.
How FMEA is used for Risk Assessment:
FMEA is a critical tool for assessing risk because it helps identify potential problems before they occur. The process involves:
Identifying potential failure modes: This involves brainstorming all the ways a product or process could fail.
Analyzing effects: Determining the consequences of each failure mode.
Assessing severity: Rating the potential harm caused by each failure mode.
Assessing occurrence: Estimating the likelihood of each failure mode happening.
Assessing detection: Determining the likelihood of detecting the failure mode before it causes harm.
Calculating Risk Rating: Multiplying the severity, occurrence, and detection ratings to prioritize risks.
Developing corrective actions: Implementing steps to reduce the RPN for high-risk failure modes.
The example below shows a sample from the FMEA for a simple fume hood that plugs into the mains:

The first failure mode considered is an overheat caused by an unintended electrical short in the device.
The effect of this failure is a possible fire
Current precautions of the fume hood design include certified electrical components and a metal enclosure. The severity of the failure is limited to (2) 'Damage that degrades functioning' since it is likely the unit would no longer operate
Since the design of the fume hood incorporates wiring according to recognized standards, likelihood of occurrence is (5) 'Unlikely'. This probability was chosen because there is still a possibility the unit could be installed on a circuit exceeding the design current ratings.
Since the wiring is located inside the product and cannot be seen by the operator, the ease of detection is 'Difficult to detect'.
The unmitigated risk rating is calculated to be 5 X 2 = 10
Acceptable risk for this product has been determined to be below a risk rating of 9 (see risk rating chart), therefore an action is required to reduce the risk associated with this hazard.
The risk reduction action was to require the customer to install a 16 Amp breaker on all circuits where the fume hood will be installed. This information was added to the installation and user documentation.
Since all wiring and components are specified to accommodate 16 Amps by design, once circuit protection is installed, the residual risk rating for this item is reduced to an acceptable level.
What is Acceptable Risk?

From a product standpoint, 'acceptable risk' is the level of risk that the organization or individuals in authority are willing to tolerate. It is subjective and influenced by a number of factors including:
Social factors: Public perception of risk, cultural values, and ethical considerations.
Economic factors: Cost-benefit analysis, economic impact of risk mitigation measures.
Legal factors: Compliance with regulations and standards.
Political factors: Government policies and priorities.
Technological factors: Available risk mitigation technologies.
It's important to note that acceptable risk can vary across different contexts and stakeholders. What is considered acceptable in one situation might not be acceptable in another. So it is critical that the company representative signing the CE Declaration of Conformity understands and accepts any residual risk associated with the product.
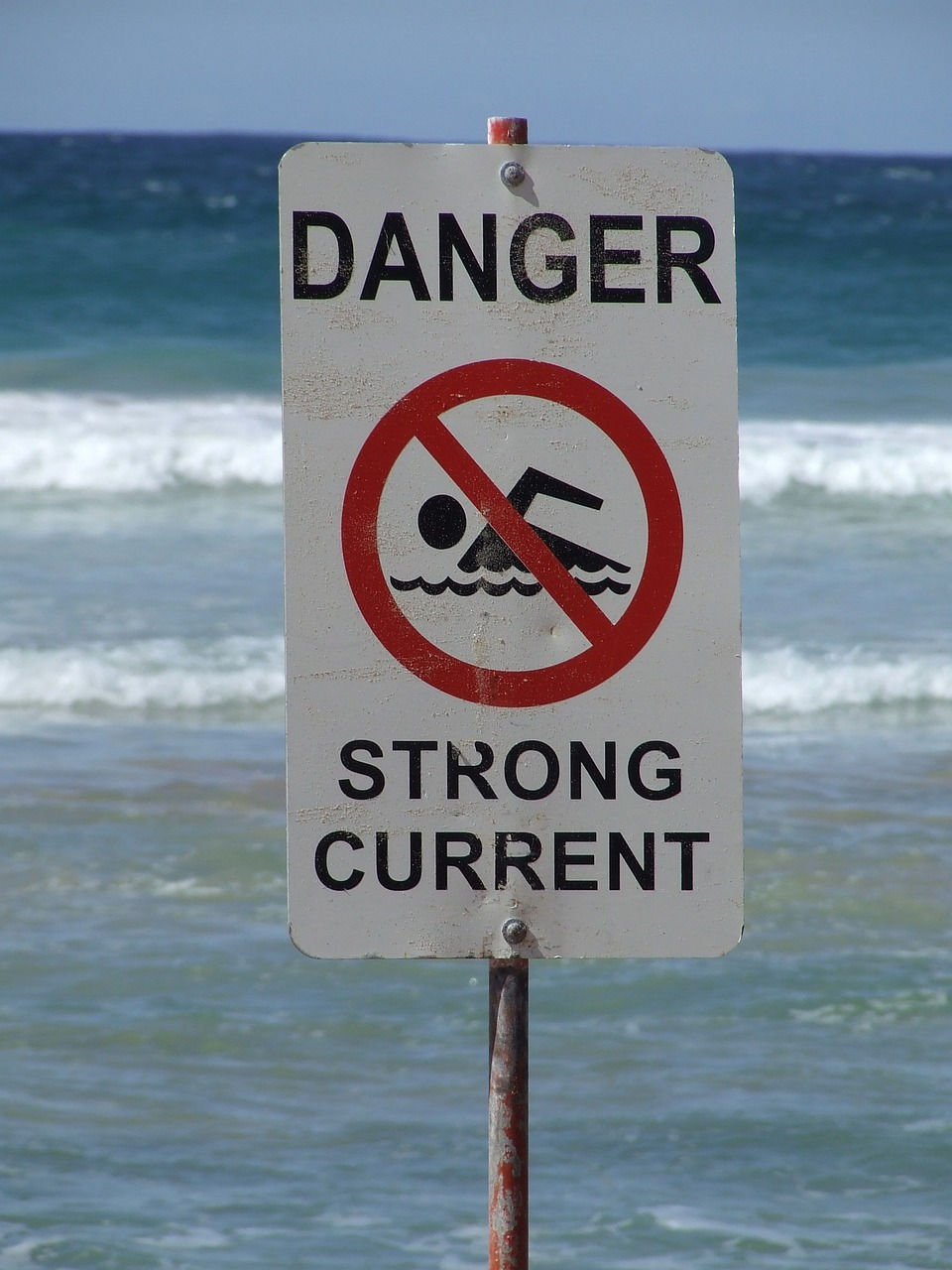
What is Residual Risk?
Residual risk is the level of risk that remains after you've implemented controls to mitigate a specific risk. This level of risk should be below what is considered 'Acceptable Risk'.
Although this risk is considered acceptable to the manufacturer, the customer may need to be informed of these residual risks to develop plans or respond to the risk if it happens.

Hazard Examples
The following is a list of common hazards encountered with commercial and industrial products. This is by no means and exhaustive list, it is intended as an example of the type of hazards to look for during risk identification.
Mechanical Hazards:
Pinch points: These are areas where two parts of a machine or product can come together and pinch or crush fingers, hands, or other body parts. Examples include hinges, conveyor belts, or closing doors.
Shearing hazards: These occur when a body part is caught between moving parts and sheared off. Examples include gears, rotating shafts, or conveyor belts.
Puncture hazards: These involve sharp objects that can pierce the skin, like exposed screws, nails, staples, or pointed tools.
Crushing hazards: These involve heavy objects or moving parts that can crush or compress body parts. Examples include falling objects, collapsing structures, or hydraulic presses.
Entanglement hazards: These occur when loose clothing, hair, or jewelry become caught in moving parts, potentially pulling the person into machinery. Examples include rotating shafts, belts, or chains.
Electrical Hazards:
Electric shock: This is the most common electrical hazard and can occur when someone comes into contact with a live electrical component.
Electrical fire: Faulty wiring, overheating components, or overloading circuits can all lead to electrical fires. These fires can cause significant damage to property and endanger lives.
Arc flash: This is a sudden and intense burst of light, heat, and pressure that can occur when a high current flows through air. Arc flashes can cause severe burns, blindness, and hearing damage and can occur in situations where a metal object, such as a tool, contacts a live circuit.
Ground faults: These occur when electricity escapes its intended path and travels to a grounded surface. This can increase the risk of electric shock, especially in wet environments.
Leakage currents: Even in properly functioning equipment, a small amount of current leakage can occur. Excessive leakage currents can lead to shock hazards or interfere with electronic components.
Liquid Hazards: Liquids can conduct electricity, increasing the risk of electrical shock if they come into contact with electrical wires or equipment. This is especially risky in wet environments.
Electromagnetic interference (EMI): Electrical devices can emit electromagnetic waves that can interfere with the operation of other electronic equipment.
Fire Hazards:
Electrical issues: This is a major cause of fire hazards in products. Faulty wiring, overloaded circuits, overheating components, and sparking can all ignite nearby flammable materials.
Open flames and heating elements: Products with open flames (like gas heaters or fireplaces) or heating elements (like toasters or clothes irons) pose a fire risk if left unattended or improperly used.
Combustible materials: Products that incorporate flammable materials in their construction or contain flammable components (like aerosol cans) can easily catch fire if exposed to heat or ignition sources.
Multiple Factors: It's important to remember that fire hazards often involve a combination of factors. For instance, a faulty electrical component might overheat and ignite nearby flammable materials, starting a fire. By identifying potential hazards and using products safely and according to instructions, the risk of fire can be significantly reduced.
Optical Hazards:
Laser radiation: Lasers of certain classes can cause serious eye injuries if viewed directly. These injuries can range from temporary burns to permanent vision loss.
Ultraviolet (UV) radiation: Excessive exposure to UV radiation, like from tanning beds or germicidal lamps, can damage the skin and eyes. This can lead to sunburn, cataracts, and even skin cancer.
Infrared (IR) radiation: While invisible to the naked eye, intense infrared radiation can cause thermal injuries to the eyes and skin. Examples include industrial heating elements or high-powered IR lamps.
Chemical Hazards:
Toxic chemicals: These chemicals can cause harm if inhaled, ingested, absorbed through the skin, or come into contact with the eyes. Examples include lead in paint, mercury in thermometers, or certain cleaning solvents.
Corrosive chemicals: These chemicals can damage or destroy living tissues upon contact. Examples include acids, bases, and some bleaches.
Irritants: These chemicals can irritate the skin, eyes, or respiratory system. Examples include chlorine fumes, pepper spray, and some household cleaning products.
Sensitizers: These chemicals can cause allergic reactions upon repeated exposure. Examples include certain fragrances, latex, and some types of epoxy resins.
Flammable liquids and gases: These chemicals can easily ignite and cause fires or explosions. Examples include gasoline, propane, and some aerosol propellants.
Asphyxiants: These chemicals can displace oxygen, causing suffocation. Examples include carbon monoxide, nitrogen, and some cleaning solvents.
Reactive chemicals: These chemicals can undergo dangerous reactions when mixed with other substances or exposed to heat, pressure, or light. Examples include pool chemicals and certain cleaning products.
Pressure Hazards:
Explosions: Products containing compressed gases or flammable liquids/aerosols can explode if exposed to excessive heat, ignition sources, or faulty pressurization. Examples include compressed gas cylinders and some paint spray cans.
Implosions: Containers designed for a certain pressure rating can implode if subjected to a vacuum or low-pressure environment. Examples include vacuum chambers and some water storage tanks.
Pressure vessel failures: Breaks or ruptures in boilers, pressure cookers, or pressurized tanks can release pressurized contents with explosive force, causing injuries and shrapnel hazards.
Leaks and whips: Leaks from pressurized systems can release fluids or gases with high velocity, posing a risk of impact injuries or exposure to hazardous substances. Additionally, whipping refers to the uncontrolled flailing of a broken hose or pipe under pressure, which can cause injuries.
Chemical or biological agent dispersal: Products designed to spray or atomize liquids or gases (like paint sprayers or crop dusters) can malfunction and release unintended amounts of the substance.
Ejection of parts: Components under pressure, like springs or pressurized chambers, can forcefully eject upon failure, causing projectile hazards.
Improper Use:
Using a product in a way not intended by the manufacturer can increase risk. For example, using an extension cord beyond its capacity or leaving flammable materials near a space heater.
Lack of maintenance:
Products that require regular cleaning or maintenance, like clothes dryers with lint buildup, can pose a fire risk if neglected.
Striper Solutions LLC, Your Regulatory Partner
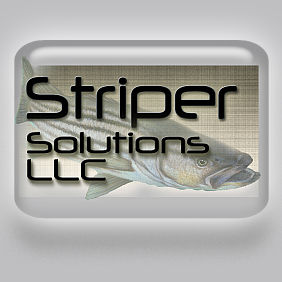
With over 30 years development experience and more than a decade providing consulting services, Striper Solutions has demonstrated a commitment to excellence and integrity in developing new products. Embracing a shift to regulatory compliance allows us to focus on a critical area of product development with the dedication and quality our customers need.
See more at www.striperllc.com
Comments